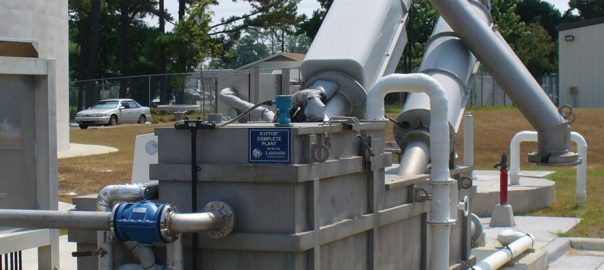
The importance of water treatment is an ongoing issue when it comes to public health and safety. Water treatment facilities and their equipment are used across the country to treat, or to remove the harmful properties from it. This is generally done by wastewater treatment plant facilities, whether publicly or privately operated. Wastewater, which is comprised of anything from toilet flushes, sinks, dishwashers, washing machines, or from industrial, commercial, or agricultural runoff. Since it can contain chemical pollutants, it is most necessary that it be treated for safe use and consumption. Facilities that clean wastewater, such as water treatment centers clean it before discharging it back into the environment. This is done through a multi step process. Let’s explore this process further.
What is Wastewater Screening?
Wastewater Screening is the first unit operation used at wastewater treatment plants (WWTPs). Screening removes objects such as rags, paper, plastics, and metals to prevent damage and clogging of downstream equipment, piping, and appurtenances.
There are different types of wastewater screens which include coarse screens, fine screens, and communitors and grinders (which are typically used at a smaller treatment facility). Screens can be made of a simple trash rack, or can be as complex as a mechanical bar system. There are also hydrocyclone systems which are devices used to separate liquids from solids, or grit from sludge, directly from the wastewater. The EPA identifies the specifications below for the varying types of screens.
Coarse screens remove large solids, rags, and debris from wastewater, and typically have openings of 6 mm (0.25 in) or larger. Fine screens are typically used to remove material that may create operation and maintenance problems in downstream processes, particularly in systems that lack primary treatment. Typical opening sizes for fine screens are 1.5 to 6 mm (0.06 to 0.25 in). Very fine screens with openings of 0.2 to 1.5 mm (0.01 to 0.06 in).
Another mechanical screen component are comminuting and grinding devices (which consist of rotating slotted cylinders) are installed in the wastewater flow channel to grind and shred material up to 6 to 19 mm (0.25 to 0.75 in) in size. There is also hydrocyclone systems. This is a system that separates liquids from solids directly from the wastewater. Heavier grit and suspended solids collect on the sides and bottom of the cyclone, while scum and lighter solids are removed from the center through the top of the cyclone.
What is Wastewater Filtering?
Wastewater filtering is another step in the process of the water treatment process. In order to safely consume water for drinking, for example, the wastewater needs to have dangerous contaminants reduced below EPA limits. To treat the water secondarily (after screening), a filtration process is used. The type of filtration system that is used depends on the facility, but a trickling filter system (also known as activated sludge process) is often used. In this process, wastewater is pumped into an area that has about the to six feet of stones, essentially into a tank that is aerated so it will produce the growth of bacteria.
On these stones, bacteria attaches to its surfaces, and then the bacteria consume and break down the matter that passes through the area. The bacteria are responsible for breaking down the organic matter among the sludge that flows into the tank. Afterward, the water goes through an additional round of treatment.
After the water leaves the sedimentation tank in the secondary stage of the treatment process, it is sent into tanks where it is exposed to chlorine (or ammonia), which can kill up to 99% of the bacteria. This is, of course, a very important step in the process.
The Difference Between Screening And Filtration
Don’t forget that there are also water filters that can be purchased for your business or home, that come in a myriad of shapes, sizes and costs. Water filters are available to support a home’s principal water resource, to attach or connect to a faucet, and they are even available for an individual water bottle, too. Water filters can be stationary or portable, depending on your usage (bathrooms, swimming pools, drinking water). While filters are an excellent resource, they do need to be maintained over time — just as equipment and a water facility does.
This might have given you a better idea of the way a water filter can be used. Now that you have this image, you can see that in the wastewater treatment process the screening is really the preliminary step that removes ‘larger’ organic matter, and then the filtering process is one that further removes any impurities.
The Wastewater Treatment Process
The wastewater screening and filtration process are crucial for creating and maintaining water that is safe for human use and consumption. There are various kinds of technology used for this process, but you can imagine that a degree of efficiency and reliability ensure the process runs seamlessly. Since water is among — if not THE — most precious resource, we must use high quality materials and a consistent, responsible process for treating it.
Water at its natural state contains undesirable sediments, colors, algae and other organisms that can be harmful. For these reasons, water treatment is a process that is paramount. To keep water treatment processes pure, equipment such as tanks, filter bed and other work areas must be clean and maintained properly. They must follow the Environmental Protection Agency’s regulations and ensure the highest standard of safety it met. When it comes to our health and safety, you want to be able to trust the screening and filtering processes that purify our water. Lakeside Equipment Corporation uses high quality materials and designs that have been engineered specifically for this process. Contact Lakeside Equipment today to find out more about how we can help you with your water treatment needs!