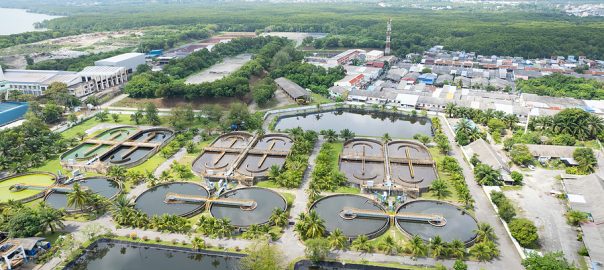
People often flush items that never should have been flushed. Menstrual products, diapers, baby wipes, condoms, and even accidental children’s toys can end up in the sewers and septic tanks and into your wastewater treatment plant.
Items like paper towels, baby wipes, and even the supposedly flushable wipes or cat litter can collect grease that goes down drains while washing dishes. It creates the fatbergs that create blockages in sewers.
Fatbergs can be gigantic and create major headaches for wastewater workers. The biggest fatberg in the U.S. to date was found in Detroit and measured 6 feet tall, 11 feet wide, and 100 feet long. This isn’t the largest fatberg found in sewers. One found in London was estimated to weigh 130 tons and stretched for over 820 feet.
It’s not just things that people put down the drain or flush in a toilet. If your district has a combined sewer overflow, which combines stormwater runoff systems and the sewer system, you’ll also end up with trash, branches, leaves, and other debris. All of these items can do a lot of damage by clogging channels and lines or getting caught on equipment. It’s important to screen incoming wastewater and septage to remove them.
Wipes Are a Costly Problem
A 2019 NACWA study looked at the added cost that baby wipes place on different states’ wastewater districts. In California, the cost came to more than $47 million. New York was second with added costs of almost $38 million. Illinois, Ohio, and Texas rounded out the top five with respective totals of $29 million, $25 million, and $25 million. In all, wipes add more than $440 million in operating costs to wastewater treatment plants throughout the country.
People in your district may not have any idea of the problem they’re creating while using wipes. Many are marked as flushable products, just like toilet paper, yet they do not dissolve effectively. Ryerson University looked at 101 brands of wipes, 23 of which were labeled flushable, and none of them broke down enough to prevent clogs.
Once in the sewer lines, wipes can increase operating costs by creating fatbergs that must be broken up and removed. At lift stations, they accumulate on screens and have to be removed, but if the bar screens are not narrow enough, they get into grinders and pumps and increase maintenance on those pieces of equipment. Wipes increase the maintenance that has to be performed on grinder pumps, dewatering pumps, mixers, and tanks.
An overloaded plant can also pose problems. If a clog has slowed wastewater from reaching your plant, you can have backups causing damage to homes and businesses. It may back up and enter the environment. If you have a sewer overflow, you face costly fines. When the wastewater finally releases as a clog is broken up and removed, you have a rush of wastewater coming into your plant. If you overload your equipment, you may have to release raw sewage, which can also lead to fines.
Wipes also drive up your plant’s disposal costs as items must be removed to containers, and trucked to landfills. You have the trucking fees, extra manpower, and disposal fees at the landfill.
The NACWA broke down what the added cost of wipes adds to a household’s sewer bill. In some areas, it’s about $5 a year, but it can be as much as $25 per year extra. This may not seem excessive, but added to other increasing expenses, it can strain households with a limited income.
There are two things you need to do. First, educate your district members about the importance of flushing only toilet paper and throwing out wipes, sanitary products, paper towels, condoms, etc. Make sure they are well aware of the problems that can drive up their annual wastewater bills. Second, install bar screens at your wastewater facility. Bar screens prevent a lot of frustration and damage in the long run.
What Do Bar Screens Do?
To reduce the damage and annoyance trash and wipes cause, bar screens are an important primary step in any wastewater treatment plan. If your plant doesn’t have a bar screen system or has an older, outdated one, it’s time to change that.
As wastewater comes into your plant, it travels through a channel and that channel has a series of coarse and fine bar screens that are usually spaced between a quarter-inch up to three inches apart. They trap items that shouldn’t be in a wastewater treatment plant, such as plastic or paper items that were flushed, animals that got into the sewers and died, and other debris like bone scraps that may get rinsed down the sink.
The bars trap the items, which could pose problems if they’re just left there. They’d block the flow of wastewater over time. That is prevented by having an automated rake that sits on the bottom of the channel and moves upward to capture all debris and some solids and lift it out of the wastewater.
At that point, the items that have been removed can go into bins to go to the landfill. Trash and hard organic materials aren’t going down the line where they can damage equipment or become extra work for your employees. The wastewater flows into the plant to begin the treatment process.
Choose a CO-TEC Screen for Easy Maintenance
The CO-TEC screens have fine and coarse galvanized steel or stainless steel bar screens that are cleaned by rake teeth that are positioned downstream of the bar screens to capture and remove trash and other debris. As all of the parts are above the surface of the wastewater, the maintenance on them is easier for your workers.
Lakeside Equipment is a trusted provider of wastewater bar screens and other crucial equipment that improves efficiency within your plant. New equipment does have an upfront cost, but the savings on the plant’s electricity bills provides a return on your investment in little time and keeps maintenance and operating costs down in the years to come. That makes the people in your district much happier in the long run.
Since 1928, Lakeside Equipment has specialized in water purification. Not only can we repair your existing wastewater treatment equipment, but our professionals offer sound advice on what you can do to improve your plant’s efficiency and avoid costly fees for improperly treated wastewater or sewer overflows.
Our team helps design the upgrades you request, keeping within your budgetary restraints, and installs bar screens that prevent problems caused by items that shouldn’t ever be flushed. Give us a call to find out more about the benefits of bar screens.
Sources:
https://www.mlive.com/news/2018/09/fatberg_metro_detroit.html