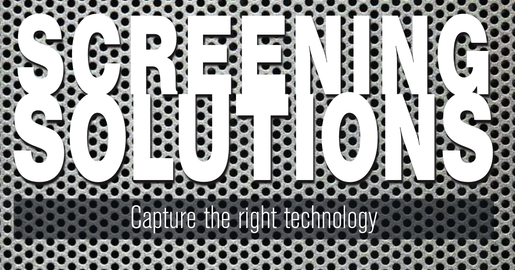
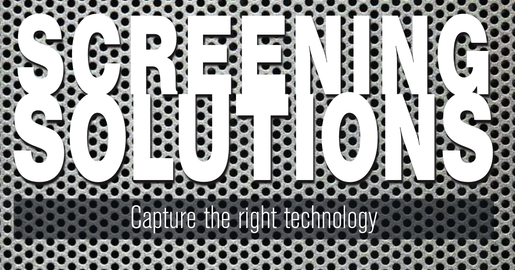
Industrial waste is cleaned before it is sent back to your company’s production lines, a local water source, or allowed to enter city sewers to go for treatment in your local waste district’s water treatment plant. As the wastewater produced in different industries can be full of pollutants, treating the water is important. The food industry may have high levels of ammonia, fat, and coliform bacteria. Power stations can have high levels of heavy metals. Treating water from these industries must be done correctly to prevent harm to people or the environment.
Managers and owners of industrial operations must carefully monitor and analyze each aspect of wastewater operations. Why? It’s important when it comes to your company’s bottom line. You need to make sure wastewater is treated effectively. You don’t want to risk releasing untreated overflow or water that doesn’t meet current guidelines for some reason. Fines for the release of untreated or poorly treated water can be costly both in terms of money and in damage to your company’s reputation. You also need to make sure you’re not wasting money on inefficient operations and excessive maintenance.
Optimizing industrial wastewater treatment is best done by paying attention to the data your systems collect. Use your operational data to look for trends and patterns in all stages of the wastewater treatment process. If you have updated wastewater equipment, it’s easy to capture data and analyze it. From there, you can predict trends, optimize your processes, and get the best practices in place for efficiency and cost-effectiveness.
What can you learn as you analyze your data? There’s a lot to be learned. An efficient wastewater treatment plant is one that handles the highs and lows, doesn’t require a lot of maintenance and repairs, and provides real-time reports to ensure water meets standards before it’s recycled or returned to a body of water. Through predictive analysis, you should be able to get a better understanding of these five areas.
First, you’re able to see what equipment is not operating as well as it can. If you have machines that are often down for maintenance, it’s costing you money. It’s impacting your wastewater treatment processes. You’ve collected data and find that one piece of equipment struggles to keep up with flow rates. Upgrading may be what it takes to have a more productive wastewater treatment system.
Second, you can track energy usage and flow rates. There may be specific times of day that wastewater rates slow down and other times when they peak. If pumps are operating at the same speed during all of these changes, it’s wasting energy. You can cut energy costs by creating systems that better accommodate the highs and lows.
Third, you’ll see where chemicals are used and if they’re being overused or not used enough. This helps keep your chemical costs to a minimum while also meeting the requirements for the water quality being released to a body of water or reused.
Fourth, you can look at the wastewater you do have and see if there are better ways to reuse it or clean it for release into the environment. Recycling wastewater is one of the best ways to keep costs down. If you could reuse water several times, you’re saving money on water bills. You don’t want dirty water impacting production. Data and analytics help you find the right balance.
Fifth, the other benefit to analytics in wastewater treatment has to do with your equipment. Say you’re seeing data that shows one pump is often breaking down and needing maintenance. You can see how much extra time and money is being spent on repairs. You’ll know if the equipment is still worth keeping or if it’s time to replace it.
Of course, there are hurdles companies face when collecting the information. If even one piece of equipment isn’t connected and communicating with the others, data will be missing. That makes it hard to get a complete picture of the treatment process and quality. Data management tools that connect everything become essential. You may need to invest in additional training so that you and your employees understand what the data means and how to use it to your advantage.
You’re probably already taking the first big step in collecting data at each key point of your water treatment measures. If you have a SCADA system like many industrial settings, you have access to important data. You’re seeing the flow rates as water comes into the screens and grit collectors. You get measurements of the pollutants in the water that’s being treated. Before it’s released, you can see the numbers and make sure they meet federal and state standards. Pair the SCADA system with modern control systems and you have all of the information you need to start analyzing your plants’ processes.
A Sharp Biological Nutrient Removal (SharpBNR) control system helps you monitor your system and adjust aeration as needed to balance the oxygen levels in the wastewater as it’s treated. The computerized control system continually monitors the system status and makes adjustments. Alarms go off if there are problems beyond the system’s scope.
SharpBNR can be partnered with your plant’s SCADA system. Within a SCADA system, you have sensors taking readings at different pieces of wastewater equipment. Readings typically include measurements for flow rates, suspended solids, pump speeds, and Dissolved Oxygen. Those readings are shown on a screen for supervisors and operators. Each screen, grit pump, basin, etc. shows yesterday’s flow and today’s flow. That data can be analyzed to look for unusual changes and peak hours.
As your system begins to analyze the numbers, it learns the necessary adjustments to effectively manage each component. You can also add motor starters and Variable Frequency Drives with the SharpBNR for optimal management. As this information is available from any authorized and connected computer terminal, you can monitor readings from your office and get alerts wherever you happen to be at that moment.
What does that mean? The system is going to be more reliable than it has been because the computer can monitor several components at the same time. Instead of having workers in different areas communicating what they’re seeing, the computer has all of the information in real-time. Adjustments are made by the computer, which continues monitoring the changes and making small adjustments until everything is running smoothly. That reduces energy costs at the same time.
You do need to keep the sensors clean so that the data that’s returned is accurate. While your maintenance team may not be doing as much on repairs, remember they’ll be beneficial at cleaning and calibrating older sensors. This ensures you have accurate information to use as you analyze your industry’s water treatment processes.
SCADA systems are great at real-time tracking and giving warnings of problems as they come up, the systems don’t do as well at predicting future problems weeks or months in advance. Smart analytics fills this gap. Analyzing the data carefully is one way to predict machines or components that are reaching their end-of-life stages.
How modern is your equipment? Would upgrading help you? If your older wastewater equipment lacks some of today’s computerized controls, it can turn data and predictive analytics into a time-consuming task. Talk to Lakeside Equipment about your current set up and learn ways to make your industrial wastewater operations more cost-effective and efficient.
Wastewater contains organic materials, but inorganic and organic solids also make their way into sewer and septic systems. How do these items get into the wastewater? It depends on the setting. Homeowners with a septic system may not realize the damage that’s caused by flushing tampon applicators or using too much toilet paper. Children may flush toys, coins, or marbles down the toilet and never tell their parents. In a city setting, items like candy wrappers or water bottles may blow into the street on recycling days and end up in storm drains.
When items like children’s small toys, plastic wrappers, and other personal products get flushed or go down a drain, it’s a problem. Whether it’s intentional or not, plastics, glass, and metal items do not break down. Items like paper towels, cigarette butts, and diapers may break down, but they do so slowly. If they’re not removed in the early stages of water treatment, it can block pipes and damage water treatment equipment. The screening process is an essential first step in any water treatment plant.
Wastewater treatment plants have screens to capture these items before they make it into grit removal systems, clarifiers, aerators, etc. Screens are also helpful in industrial settings like paper mills with wood pulp, wineries where the grape skins and pulp need to be removed before the yeast is added, or breweries where grains and hops need removal before yeast is added for the fermentation process.
Who removes the items from the screens that are getting blocked by these solids? That’s where a mechanical rake comes in. Rakes continually move across a screen to remove the items that are trapped. There are different types of rakes. One of the most efficient is the Lakeside Raptor® FalconRake® Bar Screen. How does this system work, and how does it compare to the Duperon FlexRake?
A bar screen is a vertical screening system with multiple rakes. Those rakes are on a link system that continually moves them around the vertical screen. The rakes are spaced evenly and continually rotate around the screen and tank floor. The screen captures items like plastics, sticks, logs, rocks, glass, etc. and the rakes scoop them up as it passes under the bottom of the screen. They travel up the back and are dropped into a discharge chute as the rakes pass back over the top of the bar screen. From there, items can be washed and recycled or composted, and the rakes continue in another circle to repeat the process.
When you’re looking at bar screens. There are a few things to keep in mind. First, look for construction that prevents corrosion. Stainless steel is the best. After that, you want to look at the placement of bearings, bushings, guides, and sprockets. If they’re underwater, repairs may be more common and difficult to manage. Efficiency and headroom are other factors to consider.
The Duperon FlexRake is engineered specifically to meet your demands in many of the same ways the Raptor® FalconRake® Bar Screen does. The link system can hold up to a total of 60,000 pounds, which is impressive. The links are self-lubricating, so the maintenance is minimal. Gear motors are also sealed to help prevent excessive wear. Bearings, bushings, guides, and sprockets are in higher positions to also reduce the risk of jamming, which can lead to excessive maintenance or repair. It’s also designed to avoid jams when the debris is larger than usual. If something larger goes through the screen rake, you do not have to shut it down and have someone manually remove it.
The bar screen is cleaned automatically. That makes it possible to run it 24 hours a day without having a person to operate it. It’s installed in a vertical or almost vertical position. The motor is low RPM and energy-efficient.
There are several models available. Some are better for industrial settings like food processing plants and breweries, others are ideal for wastewater plants. To find the right screen rake, you need to look at the bar opening (as small as 1/5th of an inch up to just over an inch). Look at the installation angle, too.
How does the Lakeside Raptor® FalconRake® Bar Screen compare? Much of it, including the chain link system, is crafted from stainless steel, and you get a choice. You can choose 304 stainless steel or 316. Both provide protection from corrosion, but 316 has more nickel and offers more protection in water that is chlorinated or contains more chlorides. If you treat water that has high chloride levels, consider 316 for the best protection from corrosion.
The drive system is low horsepower and incredibly efficient. Lower electricity costs in your municipality by choosing this bar screen. Variable speeds ensure comprehensive cleaning of the screen. The rake is stainless steel, and the ultra-high-molecular-weight polyethylene scraper is also durable and long-lasting. Teeth on the rake fit into the screening for optimal removal. If you’re worried about possible damage happening, don’t worry about it with this model. The bearings, bushings, guides, and sprockets are located near the top to reduce repairs from jams. It’s very unlikely that this bar screen system will need repairs. If it ever does, the drive system is above the water, which makes it much easier to manage.
With over a dozen rakes working together to remove solids, it’s an efficient removal process and headloss is minimal. It’s also adjustable, so you can space the bars to meet your needs. Bar spacing can be as little as ¼th of an inch to much larger sizes. You can also have a cover added to minimize odors. Teardrop-shaped bars are optional and reduce headloss even more. There’s also an optional weather protection system and explosion-proof design to provide peace of mind. Our Lakeside experts will help you determine the appropriate bar screen.
Where should you use the Raptor® FalconRake® Bar Screen? It’s useful in industrial and municipal settings. It’s an ideal screening system in a wastewater treatment plant. You can use it in your pump stations or sewer overflows. If you own a brewery, winery, or food processing plant, it’s good in those settings, too. As the system is customized to match the depth you need, you’re certain to have a screening and rake system that matches your needs.
Pair the Raptor® FalconRake® Bar Screen with a Raptor® Wash Press to clean, compact, and dewater the items that the bar screen removes. The Raptor® Wash Press cleans and presses the trapped materials to reduce the volume and weight of materials that go to the landfill. Lower volume and weight mean less money spent disposing of these items in a landfill. It also helps reduce the amount of waste going to the landfill.
For more than 90 years, Lakeside Equipment has provided solutions for treatment plant designers and engineers. Lakeside’s experience with water purification and water treatment processes cannot be matched. Our engineers will design a system that meets your needs and matches your budget. Our goal is to design a system that is built to last, and should you ever need parts, we have a stellar parts department who are happy to help you.
For more information on how you can achieve Lakeside quality and performance, contact one of our experts at 630-837-5640, email us at sales@lakeside-equipmnet.com or visit our website www.lakeside-equipment.com
The odors that come from a wastewater treatment plant aren’t always pleasant. People who live near the plant may start to wonder just how safe it is to have windows open and be breathing those smells all day. What about the fecal matter that’s found in wastewater? Can any of it fall on the surfaces in their home and lead to health issues? When they’re not sure, they come to your plant managers or the district with concerns.
As the plant manager, you’re not sure how to answer. Do they have valid concerns? You can’t dismiss them, so what do you tell them? Here’s what you need to know about the safety of living near a wastewater treatment plant.
So, what are the risks? Is your plant releasing bacteria into the atmosphere that makes your community members sick? It’s not likely.
A study was performed in Greece to find out exactly how much pollution impacted residents who lived near a wastewater treatment plant in Patras. The plant’s basic set-up included screens, grit chambers, outdoor primary and secondary settling tanks, outdoor chlorination, and indoor sludge treatment.
The study looked at a 1,640-foot radius and only focused on people who lived in their homes for at least eight hours per day. Once a week for an entire month, samples of the air were taken in six different neighborhoods. The samples were collected in the morning, afternoon, and evening to account for different flow rates coming into the treatment plant. Researchers also collected notes on the temperature, weather conditions, and humidity levels.
Once samples were collected, they were delivered to the processing lab within two hours. Bacteria were treated and allowed to incubate for the next 24 hours. At that point, an expert analyst looked at each to count any colonies that had formed. In bacterial colonies that did form, around 36% were Strep, 29% were Staph, 21% were not identified, 9% were E. coli, and 5% were Enterococcus. Salmonella was not found. All had less than 800 colony-forming units per cubic meter each day.
While the researchers identified airborne contaminants, there were very low concentrations. The two sampling stations that had the highest concentrations were right near the wastewater treatment plant.
This sounds concerning but consider this. An NSF International Public Health and Safety Organization study of germs in the household found Coliform on 3 out of 4 kitchen sponges or dish rags. Coliform was found on almost half of the kitchen sinks in the study. The bacteria were also found on 3 out of 10 counters and 2 out of 10 cutting boards. There were more Coliform colonies on toothbrush holders than there were on bathroom faucet handles.
Bacteria thrive in warm, moist environments. It’s why more bacteria are found in sponges than on a computer keyboard. If a homeowner isn’t constantly sanitizing their sponges, towels, sinks, and bathmats, Coliform is likely already in their home. Bathrooms and kitchens are the most common areas to find bacteria, but it’s not limited to those areas.
Coliform bacteria are not the only bacteria in the home. Pet toys and pet bowls turned out to be a significant source of Staph. Staph was also commonly found on game controllers and remotes. The five germiest items in a household were the kitchen sponge or dishrag, the kitchen sink, the toothbrush holder, pet bowls, and the coffeemaker’s water reservoir.
Go back to the days of Hippocrates for some of the earliest evidence that airborne pollutants can impact health. As early as 460 B.C., Hippocrates notes that men were becoming sick after being outside and breathing smelly air. The smells were likely from composting materials in swamps and ponds during the warmer summer months. That helped spark changes leading to more sanitary ways to dispose of those killed in wars or human waste in camps and communities.
Fast forward dozens of centuries later. Today’s wastewater treatment plants do everything possible to lower the risk of airborne contaminants. Through the use of tank covers, it can help stop hydrogen sulfide and methane from being released into the air. Covers also help keep debris like leaves, dust, and tree pollen from getting into wastewater basins. Are these covers enough, or do additional steps help reduce the risk of airborne contaminants?
You do need to start by determining where the odors come from. Check everything from the pump station to the settling tanks. It could be one specific area or several of them. Your findings help you determine the best solution. If you use open screw pumps to move wastewater from one location to the next, odors will escape. Switching to closed screw pumps stops the smells from releasing.
Some wastewater plant upgrades can help lower the odors of your plant. One of the first to consider is covers. A gas-tight cover stops hydrogen sulfide from entering the environment. Whether you choose aluminum, steel, or fiberglass, you can get retractable covers, floating covers, or flexible geomembranes. How do you choose the best one? Consider these factors.
These covers become a money-saving step to take as it also keeps algae from growing, and it adds thermal protection in the winter. When you add a gas collection cover, the methane produced during wastewater treatment is captured and can be used to heat and power your plant. That lowers operating costs.
Deodorizing misting systems throughout the plant help neutralize the smells. Another option is to start adding chemicals that react with the compounds that cause the odors. Adding an air purifying system that captures the air, filters it through biofilters or carbon filters is also helpful. Once the air is filtered, it can go out into the atmosphere without leading to unpleasant odors.
While each of these methods will help, a cover is highly effective. You may find you need multiple plans to combat odors. Don’t get discouraged. Weather extremes are changing average annual temperatures and conditions. Smells may be worse in high humidity. A windy day may make the odors travel farther than usual. If you’re having a hard time figuring it out, don’t forget wastewater equipment specialists have the answers you need.
Keeping the people in your wastewater district is one of the best ways to ensure they’re happy. If water costs are low, they’re less likely to complain. Covers are the most cost-effective solution in a wastewater treatment plant. If you don’t have covers on your tanks, you should consider them. Talk to Lakeside Equipment about equipment upgrades that help reduce odors and lower your operating costs.
Also, keep them informed. If there are more odors in the summer, explain why and assure them it’s temporary. Be honest and reassure them you’re doing everything possible to lower the smells that are emitted. Offer free tours, show why the odors occur, and listen for feedback. If you’re still not sure how to help reduce the odors that bother your neighbors, Lakeside Equipment’s specialists help you find the right solutions to incorporate in your wastewater plant design.
You’ve heard the term, but what is an Archimedes screw pump? How is it used in hydropower or waste treatment? Why is it called an Archimedes screw pump? Did he invent it? We have answers to all of your questions.
The Archimedes screw has been used for ages to move water from a place of lower elevation to another at a higher elevation. Originally, it was operated by hand. Today, the pumps can be powered by wind energy, solar power, or an electrical motor. They move more than water, though that was the original purpose.
Why is it called an Archimedes screw? Historians believe it’s because Archimedes, an Ancient Greek engineer, inventor, and physicist, invented the system. Not only did he develop the technology behind a screw pump, but he also created compound pulleys. How were people in those times using his screw pump?
How does it work? Wouldn’t gravity pull the water right back to the water source? An Archimedes screw system has a large screw that sits within a cylindrical shaft or sits in an open chute. The bottom thread of the screw sits in the lower water source and scoops some water. As the crank turns the screw, the motion forces the water to propel to the next thread.
Each turn continues propelling the water further up the screw conveyor until it reaches the place where it is deposited. As long as the motion continues, the water will keep propelling to the top and get deposited to the higher area. The speed of the pump and the width of the threads help determine how much water can be moved.
Archimedes screw pumps move more than water. They can move plastic pellets, grains, sludge, and other fluid items. If an item is fluid enough to move, a screw pump with the right dimensions and pump speeds will move them from one level to the next.
You’ve probably seen Archimedes screws at work. They’re used in snow blowers to propel the snow through the chute where it can be directed to a bank or roadside. They’re used in chocolate fountains to push the melted chocolate to the top of the fountain where it flows down the tiers and back to the heated collection pool where it travels back up and repeats the process.
You’ve likely seen farm equipment that shoots ground up corn into a farm truck where it’s transported to silos. The corn that shoots out of the raised tube reaches the top of the chute thanks to an Archimedes screw pump aka screw conveyor.
In England, there is a man-made white water rafting center called Tees Barrage. Visitors learn about white water rafting in two long courses. Four Archimedes screw pumps move close to 3,700 gallons of water each second to create the river. The pumps move the water from the lower pools to the top of the course creating close to 1,000 feet of white water before a tremendous drop. When you’re done, you can use a conveyor to follow the water back up to the top while in your raft and tackle the course all over again. As long as the pumps are doing their job, the water will keep flowing in an endless loop.
Windsor Castle’s power is supplied through Archimedes screw pumps. A 40-ton screw pump brings water from the Thames to two turbines that have gearboxes and generators to convert the energy of the water to electricity used within the Queen’s castle.
The screw pumps at Windsor Castle generate around 1.7 million kWh each year and are estimated to help reduce carbon dioxide emissions by more than 1.74 million pounds. It’s a green way to bring power to a huge castle and could easily do the same for hundreds of homes. If your town or city is looking into energy-efficient hydroelectric systems to provide power to homes and businesses, screw pump turbines are a must-have.
Archimedean screw pumps are used in waste treatment plants. As the gap between the screw blades is wide, they can cut through solids without clogging. The process for cleaning sewer and septic liquids involves several steps.
Wastewater enters the plant from trucks that pump it out at homes with septic systems or through the sewer where it’s pumped into the primary settling equipment. Screens remove some of the material, such as grease chunks, where they travel by truck to landfills. Grit is removed and also taken to the landfill. The remaining sludge is pumped into aeration tanks. Additional solids are also removed by truck. The liquid goes to another settling tank before it’s disinfected and pumped out to waterways.
What about the sludge? Archimedes screw pumps help there too. The sludge is pumped into digestion tanks where resulting methane gas can be used to provide power. Water separated from the sludge continues to aeration and disinfection. The design of a water treatment plant may vary depending on a town or city’s population and the acreage your plant has available.
They can pump stormwater, drain waterlogged land, and are useful in industrial settings where water needs to move from a low area to a higher one. A screw pump can also be a big help at separating the water from the sludge.
What about the screw pumps themselves? What are your options? There are two types of Archimedes screw pumps. If the screw is enclosed in a pipe, it’s an enclosed screw pump. With an open screw pump, the screw sits in a concrete trough and is open to the environment.
Why would you want one over the other? Enclosed screw pumps are quicker to install. You don’t have to build the trough from concrete and wait for it to cure. You could use a steel trough instead, but there is still going to be the installation time to consider. With an enclosed screw pump, the screw is already situated in a tube. It’s a quick and easy drop-in placement, which also makes for fast replacements.
An open screw pump needs space. If your water treatment plant, hydropower plant, or other business doesn’t have a lot of acreages to work with, you’ll need equipment that takes up less space.
Enclosed screw pumps come in a choice of Type C or Type S. Type C has the screw sitting within a tube that rotates. As a result, the Type C pump can sit at an angle of up to 45 degrees, which takes up less space. Type S must be at a 22 to 40-degree incline as the tube is stationary. You can opt to mount the tube on a pivot to allow it to be raised or lowered to change the pumping rate. Other advantages are:
With an open screw pump, the trough needs to be at an incline of 22 to 40 degrees. The screw has upper and lower bearings that help it rotate. There’s also the drive assembly. Self-aligning bearings can be submerged or not and keep maintenance to a minimum by having permanent lubrication to prevent wear and tear. You also gain these benefits when choosing an open screw pump:
An Archimedean or Archimedes screw pump is designed to meet your needs, but you need to consider a few factors when making your final choice. Working with an expert in screw pumps ensures you get a cost-effective design with maximum efficiency and output.
Start with the capacity you’re aiming to meet. How much liquid are you moving from one flight (level) to the next? This needs to be clear several other factors are considered in order to ensure the screw pump design matches your goals. If you pick a screw pump with too small of a screw, the capacity will be affected by the smaller diameter.
As the screw pushes the liquid up the trough or tube, the angle cannot be too steep. If you have too steep a slope, the liquid will continue to leak back to the lowest pool. Most screw tubes are set at an angle of 30 to 38 degrees, but Lakeside Equipment can get you to an inclination of 22 to 40 degrees if needed. To keep the incline at the right angle, you’ll need to have enough flights to maintain that level of incline. Your capacity increases by around 25% for each flight you add to your design.
How fast do you need the screw pump to work? If the screw isn’t rotating fast enough, the liquid will overflow and return to the bottom chamber. If it’s too fast, it can be just as wasteful. Screw speed is the number of revolutions that screw makes each minute. Finding the right screw speed helps the system remain efficient and lowers energy use. The correct horsepower helps here. You need a pump motor that lifts the liquid at the right rate and handles your desired capacity. Lakeside Equipment believes you should never choose a pump with requirements that exceed 90% of the recommended HP listed on the motor.
How deep is the level of water or liquid you’re pumping? An open screw pump will work whether or not the bottom of the screw is submerged in water.
The screw itself is something to consider. You can get screw pumps in single, double, or triple helix designs. The tighter the threads on the screw, the more fluids the screw will grab and propel upwards. A single helix has the threads farther apart so the output is lower. A good rule of thumb is to expect output to increase by 25% for each helix you add. Triple helix designs are best when you have multiple flights, and a single is best when you only have one flight.
Screw speed impacts efficiency. You don’t want to exceed the maximum screw speed or you risk cutting efficiency by increasing your plant’s electricity usage. If this happens, it’s best to install multiple screw pumps to handle the extra load.
The final factor to consider is safety. You don’t want a worker getting injured falling into equipment. Safety measures must be part of your plans. Handrails, stairs, and barriers are all important. The power controls also need to be placed so that the screw pump doesn’t turn out at the wrong time. You want qualified engineers working with you to make sure safety is a key component in your design.
Lakeside Equipment sells both open and enclosed screw pumps. Lakeside Screw Pumps are made in the U.S. and designed to be around 70% efficient, which reduces your energy use. We pride ourselves in supplying affordable screw heads that remain easy to use and maintain. Give us a call. We can help you find the right Archimedes screw pump for your needs. Reach us at (630) 837-5640.
Not every city is built on level terrain. When wastewater is at the bottom of a hill, sewage isn’t going to flow up the slope to the wastewater treatment plant magically. Instead, it collects in a basin and must be pumped up the hill through a force main. This pipe carries the pumped wastewater uphill until gravity is able to help the wastewater reach the treatment plant.
That’s one reason why someone would be looking at industrial sewage pumps. You could be a business owner and need a sewage pump for your paper mill. You have chemicals and wood pulp fibers in the wastewater, so you have to consider those factors.
Industrial sewage pumps do this, but how do municipalities and industrial sites choose the correct sewage pumps? How do you find a sewage pump that doesn’t clog, consume too much power, or need excessive hours of maintenance? Our guide to the best industrial sewage pumps helps get you started.
It’s time to start narrowing your options. Don’t focus as much on a specific brand at first. It’s better to decide what size pump is needed and the features you need. Then, you’ll need to consider your immediate budget and how much money you plan to spend on energy costs and maintenance for that pump. Ask yourself these questions.
Why Do I Need the Industrial Sewage Pump?
Your primary focus should be your goal for the sewage pump. Why do you need one? Is it for a new system, or are you replacing old equipment?
If you own a food processing plant, you may need a different sewage pump than a hotel would need. A hotel would be moving wastewater from the basement to the sewer main. But, a food processing plant is moving wastewater and materials such as animal blood, fat, or vegetable scraps.
Is It a Replacement?
Are you replacing an old, broken sewage pump? If so, was the one you had adequate for your needs or was it too small? If it was too small, it’s time to upgrade to a bigger pump. If it’s a simple replacement and the current size works for you, you could look at a similar industrial sewage pump when you’re researching.
In a growing municipality, you have to plan for additional growth, too. You might have 10,000 residents right now, but buildings are going up, and soon the population will reach 20,000. Your system must consider this growth. By planning ahead, you may pay more for equipment now, but as the population increases, you avoid having to upgrade equipment sooner than expected.
What Kind of Flow Rate Do I Expect?
How much sewage is being pumped each hour? Divide that number by 60 to get the minimum gallons per minute. You need to have an idea of the number of gallons per minute. You also have to consider the height and distance of the sewage being pumped. Lower horsepower may be cheaper to run, but it may burn out faster and require replacement sooner. If a pump says 1,150 GPM at 134 feet of max head, it could move 1,150 gallons a total of 134 feet each minute.
If it’s a small amount and isn’t traveling hundreds of feet, you may not need a pump with the highest possible HP motor. In a small brewery, the wastewater you’re pumping may only increase on brewing days. In that case, you may want to consider if you want an automatic or non-automatic sewage pump.
An automatic pump will turn itself on and off, while a worker must control the non-automatic. Generally, a non-automatic sewage pump is best when you know precisely when a pump needs to run and for how long.
Along the same lines, there are low-pressure and high-pressure pumps. Moving water from a residence to a sewer line is an example of a situation where a low-pressure pump may be best. High-pressure systems may be better in busier settings.
What Is My Budget?
You do have to consider your budget. If you’re aiming for a low-cost pump to save money, be careful that you’re not going to end up spending more on maintenance each year. The same is true of an expensive pump. A higher price doesn’t guarantee longevity. That’s why it’s best to work with a company that will help you get the best quality for your budget.
If you’re worried about the cost, you should also think about ways to save money. Solar panels are an initial investment, but tax incentives may make them worthwhile. The savings on energy can pay for the cost of the solar panels in just a few years. Wind power is another option if you’re looking to invest in renewable energy.
Could a Screw Pump Be the Best Choice for Industrial Sewage?
Archimedes screw pumps have the power to move sewage at a constant speed without clogging or needing a grinder pump. They can be up to 75% efficient, which lowers electricity bills. They’re suitable for moving wastewater in an industrial setting and come in two types.
How does a screw pump work? Some systems have a pool or trench at the bottom for the sewage or wastewater to pool. The screw turns and propels the water up the blades of the screw. Once the sewage reaches the top, it deposits the liquids out of the top of the trough or chute.
Not every industrial setting is best served by an Archimedes screw pump, but if you could use one to move your sewage, it’s a cost-effective, trouble-free system to consider. If it would help you, the best screw pump design is determined by your available space and the reason for the sewage pump.
Choosing the best industrial sewage pumps isn’t a decision to rush. To ensure you get a pump that will last and not consume ridiculous amounts of energy, ask an expert in wastewater technology for advice. You don’t have to have the answers. You can turn to the pros to help you find the best industrial sewage pump. If you need an entire system designed or components upgraded, there’s no better place to start than with Lakeside Equipment.
Lakeside Equipment has a team of engineers ready to help you with your industrial wastewater system design. Our company started back in 1928 and has specialized in water purification ever since. Call us to learn more about our line of Archimedes screw pumps and other water treatment equipment.
Water treatment dates back to at least 4000 B.C. Ancient Greek documents discussed purifying water by running it through charcoal, exposing it to the UV rays of the sun, and boiling it prior to consumption. This was done to kill bacteria, remove odors, improve taste, and eliminate cloudiness.
There are also historical records showing that Ancient Egyptians added alum to water to help clarify it by suspending the particles floating in it. In the 1800s, the cholera outbreak in London was found to stem from sewage that got into a well used for drinking water. Louis Pasteur would be the person to show how bacteria in the water could cause disease in people.
Our water today is cleaner because of the world’s history and discoveries along the way. Today, activated charcoal, or activated carbon, is one of the components used in water filtration systems. In 2017, activated charcoal was a major player in water filtration, but substances like olive pits, shells from nuts, and coconut fibers are also being used. Before the year 2025 ends, it’s expected that the global activated carbon market will be worth more than $6.6 billion.
You’ve heard of the term absorb, which is to soak something up. Activated charcoal or carbon is a little different. It adsorbs odors and substances from liquids. Instead of absorbing these odors and substances, it bonds to them. That’s called adsorption.
A process using oxygen turns charcoal very porous. Those tiny pores trap and hold the substances that cause off-colors and odors in water. It can trap and hold things like chlorine, toxins, and even some prescription drugs that make their way into water sources.
In a household, you might have a water purification system like Brita or PUR that attaches to your faucet or a water pitcher and removes impurities and odors from your tap water. People often use them to remove the chlorine odor and taste that remains in public drinking water.
In a water treatment plant, crushed activated carbon or charcoal can help remove excess chlorine, organic materials, and other impurities. To do this, the crushed carbon is added right to the water where it removes the contaminants and then is removed after it settles with other sediments in holding tanks. Once it is removed, it can move to compost areas or landfills.
Sometimes, activated carbon pairs with a UV disinfection system to aid in the removal of chlorine and other compounds that affect the taste and smell of water that’s been treated.
The Environmental Protection Agency lists two ways to implement an activated carbon filtration system in a water treatment plant. One is a granular activated carbon filter that is added after the rapid mix, flocculation/sedimentation, and filtration steps. Water flows into the granular activated carbon filter once the water has been in the filtration tanks. This is known as post-filtration adsorption.
The second placement is as part of the filtration tank. The granulated charcoal sits in the bottom of the filtration tank where it filters out odors and other contaminants. In this type of system, you have the rapid mix, flocculation/sedimentation, and filtration.
Regulations on water quality and purification change regularly. At the moment, the EPA has regulations in place for more than 90 contaminants. The public can request that it gets added to the Contaminant Candidate List (CCL). This request list is published at EPA.gov and accepted nominations for additional contaminants at the end of 2018. Verdicts on whether or not the contaminants were added or not are also published on the EPA’s site under Current and Previous CCLs.
The last update for the National Primary Drinking Water Regulations was released in 2009. As more items are added, water filtration plants have to keep up with the changes and make sure their equipment and tests look for those new contaminants. Activated carbon filtration often helps remove some of these new contaminants.
Lakeside Equipment has one piece of equipment that’s an essential part of any water treatment plant. Look into the stainless steel or PES filter cloth screening that’s part of the MicroStar Filter. This final step in water treatment runs your cleaned water through the filter cloth and backwashes any remaining contaminants into a central hopper where it is discharged. It’s an energy efficient step in the final stage of water filtration.
Learn more about the MicroStar Filter and Lakeside Equipment’s other clarification and filtration equipment. Our experts can help you find the right water filtration system at the right price. We’ve been in the water filtration business for more than 90 years and are happy to share our expertise with you. Call 630-837-5640 for more information.
In some towns and cities, wastewater treatment plants take care of more than wastewater that comes in from the sewers. Rural neighborhoods and villages may be near a city, but they’re too far to connect to the main sewer lines. The home’s wastewater goes into septic tanks at those houses, where it sits for months or years until it’s pumped out and hauled to a septage acceptance plant.
Over 26 million U.S. homes are on a septic system rather than a sewer. Maine and Vermont are leading states, with more than half of all homes being too far from sewer lines. Instead, septic systems are installed underground in the homeowner’s yard. Have you ever wondered how septage is processed or how these systems work?
In city homes, you flush the toilet, run the dishwasher, do the laundry, or take a shower. That water leaves your home through pipes that travel to the main sewer lines. Rural homeowners don’t have that option. Their residences are too far from sewer lines to make it cost-effective to connect to them. Instead, their home’s main septic drain pipe travels through the basement wall or crawlspace and connects to a baffle box leading to a large concrete, fiberglass, or plastic vessel known as a septic tank.
Once the wastewater is in the septic tank, fecal matter and small food particles sink to the bottom, where bacteria break them down into sludge. Oils and fats (scum) float to the top, trapping the liquid sewage between the sludge and the scum. There’s an effluent filter and L-shaped pipe positioned just below the level of the liquid sewage. The liquids travel through the effluent filter and exit through a system of pipes that lead to a leach field.
The leach field is a series of perforated pipes over a porous liner or layer of crushed stone that allow the liquid waste to soak through the base material, filtering out some bacteria, and traveling deeper into the soil. As those liquids travel through the soil layers, the sand and rocks filter more of the bacteria. Eventually, any remaining purified wastewater ends up in the groundwater. This is why regulations require septic systems to be a reasonable distance from private wells.
Not every home has enough slope for liquids to travel into the leach field, or the ground may not drain quickly enough. In that case, a mound system is installed to use pumps to move the wastewater through filters and the manufactured mound before it travels down into the soil and groundwater.
If wastewater isn’t draining fast enough due to a blockage, flooding, or an overfilled septic tank, it can lead to overflowing toilets, sinks, and washing machine drain pipes. It can also cause raw sewage to puddle on the ground. To prevent pollution, homeowners hire local septic companies to pump out septic tanks every few years or less. Three years is the recommendation for the average four-person household. Larger households, duplexes, or apartment complexes need to have their septic tank pumped out more often.
Trucks use suction and hoses to pump out the tank into the back of a septic company’s truck. That hauler will pump out the wastewater from multiple houses and travel to an independent septage pump station or a water treatment plant. There, the wastewater gets filtered, disinfected, and returned to a body of water or a public water system.
Septage is a mix of solids, oils/fats, and wastewater. The waste and fats must be separated from the liquids, and that’s one of the first steps when the wastewater reaches a treatment facility. The amount of septage that’s processed impacts the equipment that’s used. A small community may not need as large a system as a facility that serves an entire county.
The wastewater is pumped out of the truck and into the septage treatment or wastewater treatment plant’s screens and grit removal system, where solids and liquid sewage start to separate. Grit removal is used to remove things like coffee grounds that got into the coffee pot, sand, and other fine particulates that may go down the sink when items get washed, or people take showers.
Containers capture these solids where they can be incinerated to create energy or heat. In some areas, they are used as fertilizer. The grease and oils may stick to the walls of the tanks, so that needs to be removed. Scum also needs to be skimmed from the surface and removed from the processing tanks. System designs may include equipment that automatically skims the surface and removes those fats.
The remaining water is aerated to allow bacteria to start breaking down contaminants. Chemicals may be used to help kill any remaining bacteria. The use of chemicals will vary from one plant to the next. If chlorine or similar chemical agents are used, UV is one way to remove excess chlorine before the wastewater goes to water sources or back to homes.
A smaller independent plant may use lime to help the initial process of drawing the water from the solids. Filter presses, sand, or vacuums can also be used to separate the liquid waste from the solids. Odor control is essential as no treatment plant wants to become a nuisance to the neighbors. Enclosed tanks and treatment equipment also keep odors to a minimum.
Talk to Lakeside Equipment about your wastewater treatment plant’s needs. If you accept septage or want to add the equipment in order to receive it, we’re the experts you need to work with you and make it happen. We have a couple of options.
A Raptor Septage Complete Plant is an all-in-one plant with that screens, removes grit, and can aerate the septage. It’s an all-in-one system that’s ideal for treating wastewater and solids at an independent septage treatment plant. You can even add a grease trap and skimmer for efficiency.
Benefits to the Raptor Septage Complete Plant include:
A Raptor Septage Acceptance Plant provides the equipment needed for wastewater treatment plants that handle wastewater trucked in from rural communities and that arrives through sewer lines. It pre-treats septage before it’s mixed into the wastewater coming from businesses and households through the sewers. An optional Acceptance Control System allows haulers to print out reports of the septage they uploaded at the facility.
Benefits to the Raptor Septage Acceptance Plant include:
Let us know your vision and budget. Our experts are happy to discuss the best options and supply the engineers and installers to ensure the upgrade at your wastewater treatment plant goes smoothly.
The Federal Water Pollution Control Act changed how wastewater discharge was handled. The goal was to help keep biological and chemical contaminants out of U.S. waterways. Over the years, changes were made. They included:
Each time the rules change, municipal water treatment plants need to make sure they can meet the new guidelines and rules. The U.S. EPA says that many wastewater and treatment facilities have outdated equipment that requires repairs or replacement.
It’s getting harder for wastewater treatment plants to keep up with the growing population and changes to wastewater pollutants. It’s estimated that 33% of new developments require systems such as septic systems. It’s the only way states can keep up with the growth and spread from cities with wastewater treatment plants.
To make sure they meet the current laws and regulations, make sure your municipal water treatment plans are kept up-to-date. Before you make changes, read these tips to make sure you’re making the right decisions.
It does cost a lot of money to replace the equipment in a wastewater treatment plant. That said, how much are you spending on repairs each year? Are you able to keep up with the demand? Has your equipment failed and created spills that led to fines?
While it can cost money to purchase and install new wastewater equipment, you can end up saving money. You won’t pay as much in emergency maintenance. It will cost less to run the equipment and production increases. In little time, you’ll recoup the money you’ve spent.
In your municipality, are you able to meet the needs of a growing population? If not, it’s time to expand your plant. You don’t want your wastewater treatment plant to become overloaded. When you expand, it may be worthwhile to build a system that’s larger than you need. This accounts for future growth, too.
If you can’t expand due to a lack of space, you can look for machines and technologies that increase capacity without taking up more space. For example, Lakeside’s H-PAC system is designed to take up less space while also reducing operating and engineering costs. You’ll be able to do more without having to build additions and buy up land for the expansion.
It’s estimated that water treatment plants and the water industry use as much as 4% of the nation’s energy. With demands for better wastewater treatment plans, there are also concerns over the cost of electricity. The EPA estimates that up to 40% of a municipality’s budget is for the wastewater treatment plant’s electricity. Public water systems usage of electricity accounts for as much as 80% of a municipality’s budget.
To keep from blowing a budget, there’s a need for wastewater treatment plans to look at the equipment that reduces operating costs. Water treatment is going to use energy. You have pumps and equipment using electricity 24/7. You can do your part by looking into equipment that can do the job correctly for the lowest operating costs.
Think about the last time the regulations shifted. Were you able to meet the changing regulations with ease or was it a struggle? Taxpayers often balk when it comes to increasing town and city budgets by a large percentage, so you have to consider their ability to pay more in taxes, too. Upgrading equipment is one solution, but you might be able to make improvements with some modifications to your existing plan or by modifying your water treatment plant’s buildings. One of the easiest ways to decide is by working with professionals who are ready to help you find economical solutions.
Lakeside Equipment specializes in the design and installation of water purification systems for companies and municipalities. We also help you find the parts you need for your older equipment. With more than 90 years in the industry, you can trust Lakeside to find you the best solutions for your water treatment plan.
Let us know more about your goals. We can help you come up with the best plan for your budgetary needs. Give us a call today at 630-837-5640.
Wastewater treatment plants fill many roles. The water that’s treated and released to bodies of water must be treated in a way that protects fish, shellfish, and other wildlife. If it goes back into the drinking water supply, it must be safely treated before the public consumes it. It also has to protect the general public who swim in water coming from treatment plants.
The EPA sets water quality standards for all wastewater treatment plants to meet. If a facility fails to do this, it can lead to fines and negative press. For this reason, experts in wastewater continue to look for ways to improve wastewater treatment. With more than 30 billion gallons of water treated every day, things still can slip through the cracks. Here are some recent discoveries that can help return cleaner water to the environment.
When ground, the shells of crabs, lobster, and shrimp create a fibrous substance that binds to things. It’s touted as helping with wound care as it causes the blood to clot. It’s also studied as a means for lowering cholesterol levels in the blood. People with high blood pressure use it as a salt substitute.
The company Tidal Vision is researching the use of chitosan to create a liquid solution that removes metals like iron and copper from stormwater runoff and wastewater. It reduces the amount of waste going into landfills, and it can reduce costs as this is a substance that is thrown away by seafood manufacturers and restaurants every day.
Researchers are studying beneficial magnetic nanosponges in water treatment, especially when treating wastewater in agricultural settings. Microscopic holes allow molecules to travel through the sponge-like structures at record speeds. Not only is this helping with efficient water treatment, but it’s also aiding with the capture of fuel from the wastewater treatment process.
In the study, a 75% mixture of magnetic nanosponges excelled at removing contaminants in the sedimentation tanks and farm pits where the tests were run. Nanosponges speed up that reaction time by 6x, allowing optimal water treatment. This improves efficiency and is more cost-effective than current wastewater filtration steps.
Until now, sponges haven’t had the ideal pore sizes for the split of hydrogen and oxygen, which impacts how well plants can convert the CO2 into fuel that can be used for things like heating a facility. With the use of nanosponges, the optimal pore sizes aid the division, so the structures prove beneficial both at cleaning wastewater and converting the gases to usable fuel.
Stop and think about the results of wastewater treatment, and we’re not talking about the cleaned water that can return to public water supplies or bodies of water. Plants create greenhouse gases, such as methane. Methane is often burned to heat or power plants, but that produces carbon dioxide that’s released into the environment. Carbon dioxide may not smell like methane, but it’s still harmful to the environment.
Researchers in Arizona have been studying the benefits of using microalgae to process these greenhouse gases. The microalgae are in ponds and feed on methane and carbon dioxide that results from wastewater treatment.
As the algae feed on the gases, methane is captured as a more valuable form of biomethane for power and heat. The carbon dioxide is fully ingested and helps the algae multiply. The excess algae are rich in omega-3 fatty acids beneficial in food products for both animals and humans.
One area that has been researched for several decades is microbial ecosystems. There are thousands of microbes, and newer discoveries improve water treatment steps. While aeration is one of the most common steps in wastewater, it also uses a lot of energy. As much as 80% of a plant’s operating costs are linked to aeration.
Microbial ecosystems help by eliminating some of the chemical additives and excessive use of aeration. Lowering chemical additives helps lower the amount of nitrogen and phosphorus in wastewater sludge.
In the 1990s, researchers discovered anaerobic ammonium oxidation bacteria (anammox) could convert ammonia in waste and farm runoff to nitrogen gas. While some aeration was still required, the amount was far lower.
The microbes took up space, but that issue was resolved by introducing granular pellets that required 25% less space and helped lower operating costs by as much as 30%. A Dutch town became the first to embrace the microbe pellets for both industrial and residential wastewater, and it was successful in both areas.
Research on microbial ecosystems didn’t stop with that project. A Danish university uncovered a new type of ammonia oxidation bacteria known as comammox in 2015. Comammox was a massive discovery as they could process the ammonia without requiring any oxygen. However, testing is still ongoing to see if they can eliminate the need for aeration in wastewater treatment facilities.
A California company specializing in oxygenation is rapidly expanding the use of equipment that creates nanobubbles to aid in water treatment. Moleaer is investing $9 million to work with universities across the country to study all of the benefits and uses of nanobubbles in food manufacturing, wastewater treatment, and agriculture.
While aeration is a critical step in wastewater treatment, most mixers stir and aerate with the bubble sizes you’d expect in water. Nanobubbles are tiny. They’re so little, you cannot see them. In fact, nanobubbles are reportedly more than 2,000 times smaller than a grain of salt. Due to their size, they remain in the water for longer, increasing the amount of oxygen within the water.
A professor at UCLA reported that nanobubbles could transfer oxygen at rates of 85%, which is far greater than the typical average of 2%. When this technology is used, it can reduce the need for chemicals in wastewater treatment and reduce operating budgets.
Polyhydroxyalkanoates (PHAs) are a polymer that bacteria can produce when they digest sewage. This is an important study as PHA can be converted into biodegradable plastic. A plant in the Netherlands is currently researching the use of bacteria to create PHA bioplastic that can be used in manufacturing in areas where a water-resistant, flame-retardant biodegradable composite is needed, such as construction materials.
Researchers at the National University of Singapore came across a new strain of bacteria that proved effective at removing nitrogen and phosphorus from raw sewage. The microbe named Thauera sp. strain SND5 was found in a wastewater treatment plant, but it behaved differently, catching Associate Professor He Jianzhong’s attention.
Bacteria are already used in wastewater treatment to purify the water, but most can handle one compound. SND5 was the first bacteria he’d seen that was able to multitask. Because this bacterium can take care of both nitrogen and phosphorus simultaneously, it has the potential of being more effective at a lower cost.
Research is ongoing, and discoveries occur each year. What can wastewater treatment plants do in the meantime? One of the best steps to take is to do a walkthrough of your plant’s equipment to explore the equipment’s age, how often it breaks down or requires maintenance, and what’s driving your plant’s utility costs up.
When you sit down and look at every aspect of your wastewater treatment plant’s operating costs, successes, and failures, it helps you realize where there is room for improvement. That’s when you talk to an expert in wastewater treatment plant equipment and design.
Lakeside Equipment’s experts help you find ways to improve performance, lower costs, and enhance efficiency. Call us to schedule a consultation.